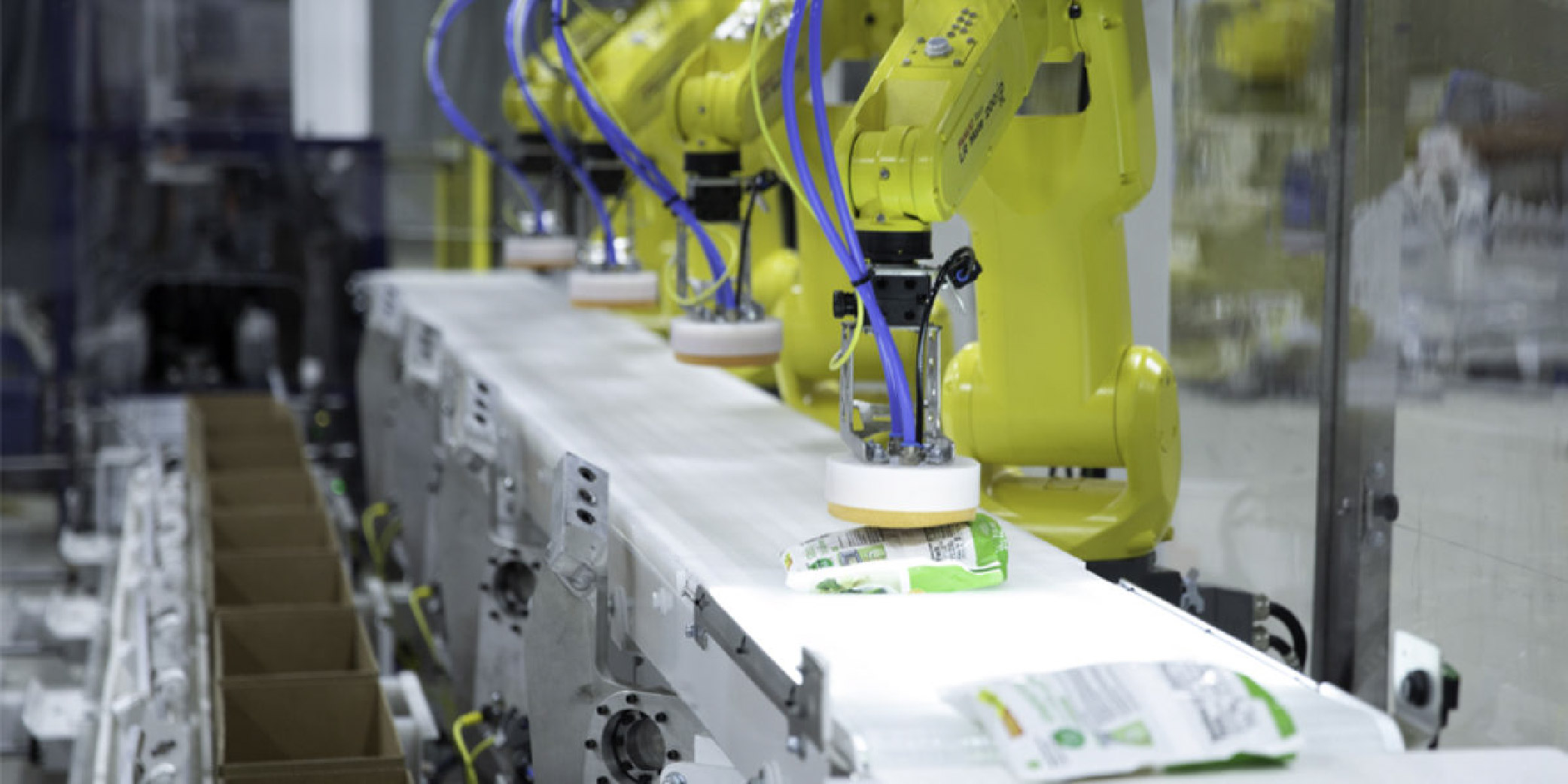
Robots are indispensable in the food and beverage sector due to their speed, accuracy and reliability. Now, with vision guidance, they’re reaching new levels of productivity.
Vision guidance uses cameras to identify objects within the robot’s work area and adjust target coordinates in real time, enhancing both primary and secondary packaging operations. In this blog, we explore how this game-changing technology is benefiting the food and beverage industry.
The Locating and Grasping Challenge
Delta, SCARA, and articulated robots used in packaging excel in repeatability, precisely following their programmed paths. However, in primary packaging, this becomes a challenge when products vary in size, shape and orientation.
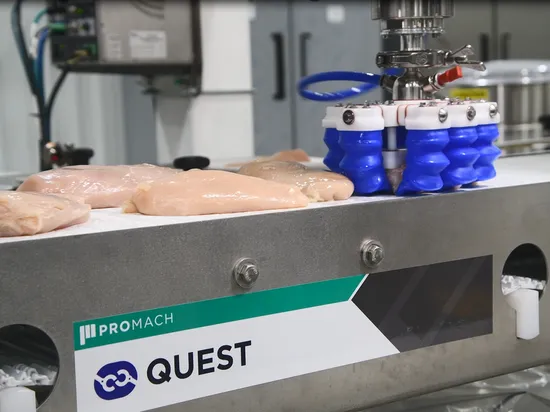
For consistent positioning and grasping, the robot must determine the exact location and dimensions of each item before picking it up.
While secondary packaging is generally more predictable, since products have defined shapes and sizes, some packaging, like pouches, can still vary significantly. Even in these cases, a robot without vision guidance relies on precise, repeatable positioning to execute pick-and-place operations effectively.
The Transformational Impacts of Vision-Guided Robotics
Vision guidance technologies help robots accurately locate objects to grasp and position them within enclosures. The best choice depends on the application, but in many cases, 3D imaging offers the most reliable solution.
The setup typically involves mounting one or more cameras with appropriate lighting above the infeed and/or outfeed systems. Advanced software then analyzes the images, calculates offsets from programmed coordinates, and transmits precise adjustments to the robot.
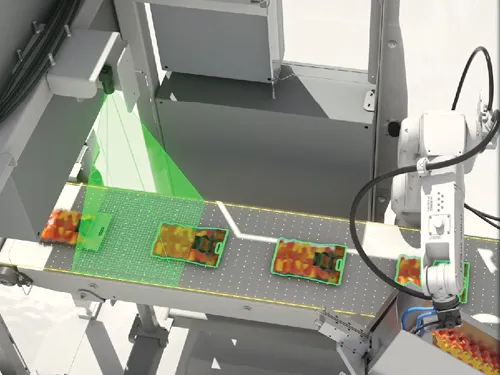
Here are five key ways vision-guided robotics (VGR) enhances packaging operations:
- Enhanced Quality Control & Consistency
- Flexibility for Different Packaging Configurations
- Speed & Throughput Improvements
- Sustainability & Waste Reduction
- Operational Benefits
Let’s explore each of these in detail.
1. Enhanced Quality Control & Consistency
Traditional case packing relies on complex infeed systems to align products. Vision-guided robotics eliminates the need for these setups altogether. Instead, vision-guided robotics identify, locate and pick each item based on its unique position and orientation.
The same applies to loading products into primary packaging. If an item is slightly skewed, the system automatically adjusts the pick point, ensuring precise placement in its enclosure or case.
This automation reduces the need for workers to monitor and manually correct infeed and outfeed issues, making packaging operations less hands-on and improving workplace safety. Companies using VGR often find they can operate with fewer workers while also reducing turnover, as the work becomes less frustrating and more efficient.
Additionally, integrated camera systems can detect packaging defects in real time, ensuring only high-quality products reach consumers. By catching issues during packaging rather than after, businesses minimize waste and rework, saving both time and materials.
2. Flexibility for Different Packaging Configurations
Some traditional case packing equipment requires lengthy changeovers and significant downtime when switching to a different pack format. While robotic handling improves flexibility, operators still need to fine-tune positions and verify results.
Vision-guided systems, however, adapt seamlessly to varying package shapes, sizes and orientations without extensive reprogramming or setup. This capability is especially valuable for manufacturers managing multiple SKUs or seasonal packaging changes.
By reducing downtime and streamlining transitions, VGR helps improve key performance metrics like overall equipment effectiveness (OEE) for the food and beverage industry.
3. Speed & Throughput Improvements
SCARA and delta robots are capable of high-speed packaging with impressive accuracy, but faster production can increase the impact of any stoppages.
Vision-guided robotic packaging addresses this challenge in three key ways: changeovers are quicker, microstoppages (brief pauses to resolve issues) are minimized, and manual adjustments are no longer needed. The outcome is improved productivity and higher throughput.
4. Sustainability & Waste Reduction
Precision, vision-guided packing minimizes waste of products, packing materials and other resources. This is achieved through optimized case fills, reduced use of fillers and the avoidance of over-packaging.
Additionally, fewer errors, less rework and a reduction in unplanned downtime all contribute to lower overall resource consumption.
5. Operational Benefits
Vision guidance eliminates the need for precise product and container positioning, preventing small stoppages that negatively impact OEE and related metrics. It also speeds up changeovers, creating additional production capacity for food industry manufacturers.
The system’s ability to detect packaging defects as they occur allows for quicker corrective actions, reducing the quantity of nonconforming products produced and packed. This not only saves on material waste but also reduces downtime.
Finally, these improvements in operational efficiency lead to two additional benefits: lower maintenance costs and reduced energy consumption.
Take Packaging Operations to the Next Level
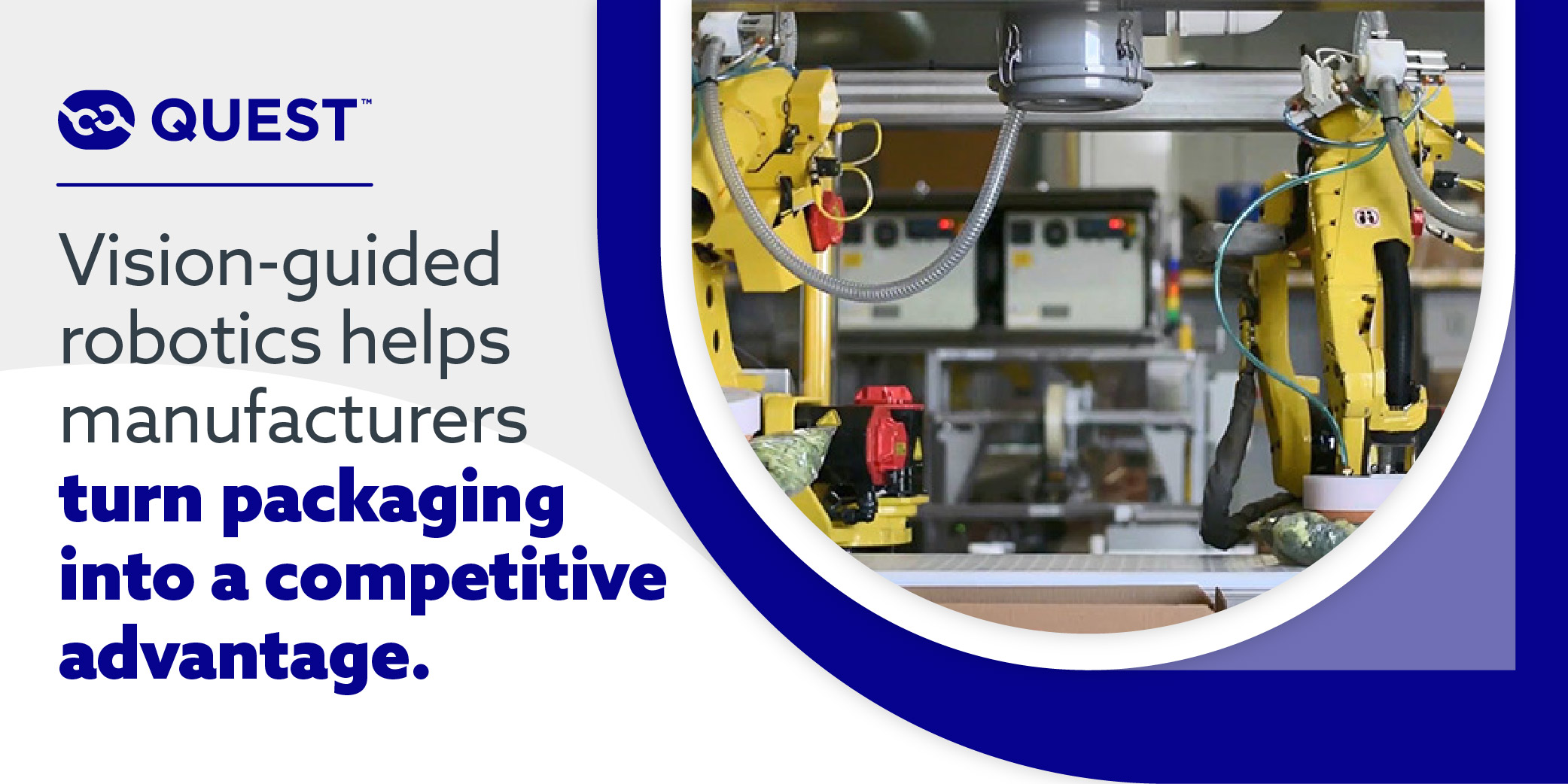
Packaging plays a crucial role in a product’s success. It not only protects the product but also enhances its visual appeal.
However, packaging — both primary and secondary — can often lead to inefficiencies and increased costs. By integrating vision-guided robotics, Quest customers turn packaging into a competitive advantage.
We understand that a company’s reputation depends on the quality of its packaging. That’s why we offer advanced vision systems as part of our robotic packaging solutions. With these systems in place, manufacturers can trust that industry-leading technology is packaging their products with precision and consistency.
Ready to optimize your food and beverage packaging operations? Contact us today to start a project or get your questions answered.