It’s been half a decade since the onset of COVID-19, and yet food production standards remain at an all-time high. There are heightened expectations of hygiene and best practices for production companies, with a consistent influx of new regulations and preventative measures enacted for public safety.
This is particularly true of high-risk sectors such as dairy, which require an even heavier emphasis on purity and sanitation. This coincides with increasing demand: The U.S. alone produces more than 600 million pounds of milk per month, which is used to create millions of pounds of yogurt, butter, cheese, and more.
With an increase in demand over the following five years, dairy producers around the country are adopting modern sanitation solutions to address demand.
The modern dairy producer needs cutting-edge, sanitary solutions to both meet and exceed increasing regulatory and customer standards. This is the reason why thousands are switching to vision-guided automation robotics. It’s one of the simplest and most effective ways to package and protect dairy products.
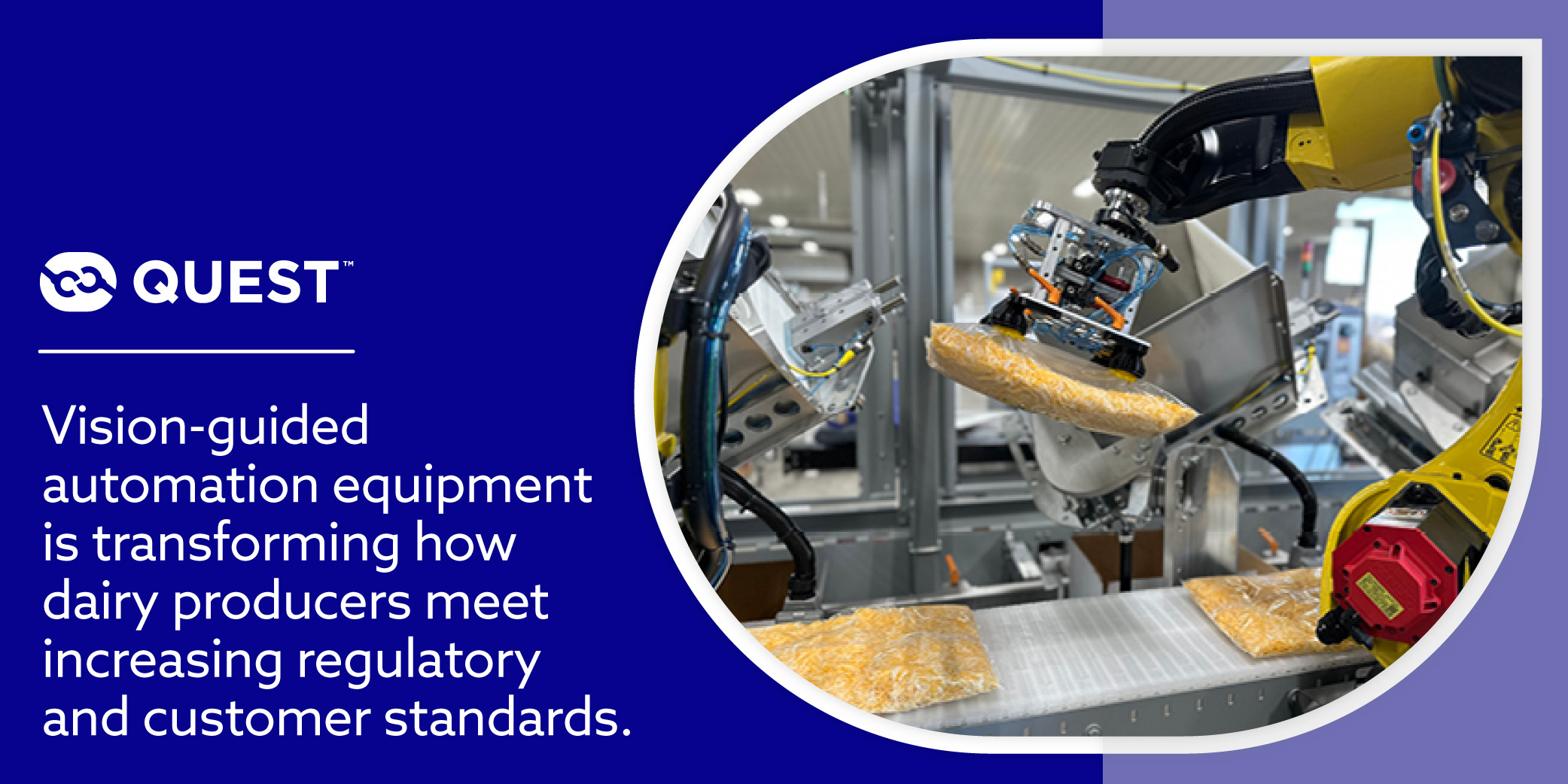
It’s been half a decade since the onset of COVID-19, and yet food production standards remain at an all-time high. There are heightened expectations of hygiene and best practices for production companies, with a consistent influx of new regulations and preventative measures enacted for public safety.
This is particularly true of high-risk sectors such as dairy, which require an even heavier emphasis on purity and sanitation. This coincides with increasing demand: The U.S. alone produces more than 600 million pounds of milk per month, which is used to create millions of pounds of yogurt, butter, cheese, and more.
With an increase in demand over the following five years, dairy producers around the country are adopting modern sanitation solutions to address demand.
The modern dairy producer needs cutting-edge, sanitary solutions to both meet and exceed increasing regulatory and customer standards. This is the reason why thousands are switching to vision-guided automation robotics. It’s one of the simplest and most effective ways to package and protect dairy products.
There are also tools like the Quest Box Bot QB300 series robotic palletizer, which can prepare products for shipping within stainless steel designs. These are USDA Dairy compliant and specifically designed for wash-down environments such as dairy packing facilities.
Sanitary Design Considerations for Robotic Equipment
Not all automation equipment is “sanitation-ready,” despite seeing marketing collateral to the contrary. It’s important to reference the USDA’s compliance and material selection to ensure the safest and most efficient solution for packaging dairy.
A few things that make robotic equipment safe for dairy packaging include:
- Food-grade coatings: This should include smooth surfaces without visible or non-visible crevices. Quest’s Qleen Coat Robotic Coating is a popular option that enhances both durability and sanitation.
- Easy disassembly for cleaning: Dairy products are often difficult to clean and require specialized equipment. The componentry you purchase should be easy to disassemble for thorough cleaning on a regular basis.
- Sanitary joinings: The connections between “End Of Arm Toolings” (EOAT) and the “dressing” (hoses and cables) must be sanitary, easy to clean and prevent bacterial harborage. All surfaces must also be inspectable by health professionals and programmed for specific positions to ensure dairy products are safely handled.
Keep in mind this barely scratches the surface — you may need to follow additional guidelines depending on your industry. It would be wise to connect with a dairy and robotics safety specialist to get more information about regulations for your use case.
Features of Sanitary Robotics in Action
There are dozens of sanitary robotics options on the market. But how can you be sure which one(s) to choose? Below are some must-have features of robotic systems built with dairy safety in mind:
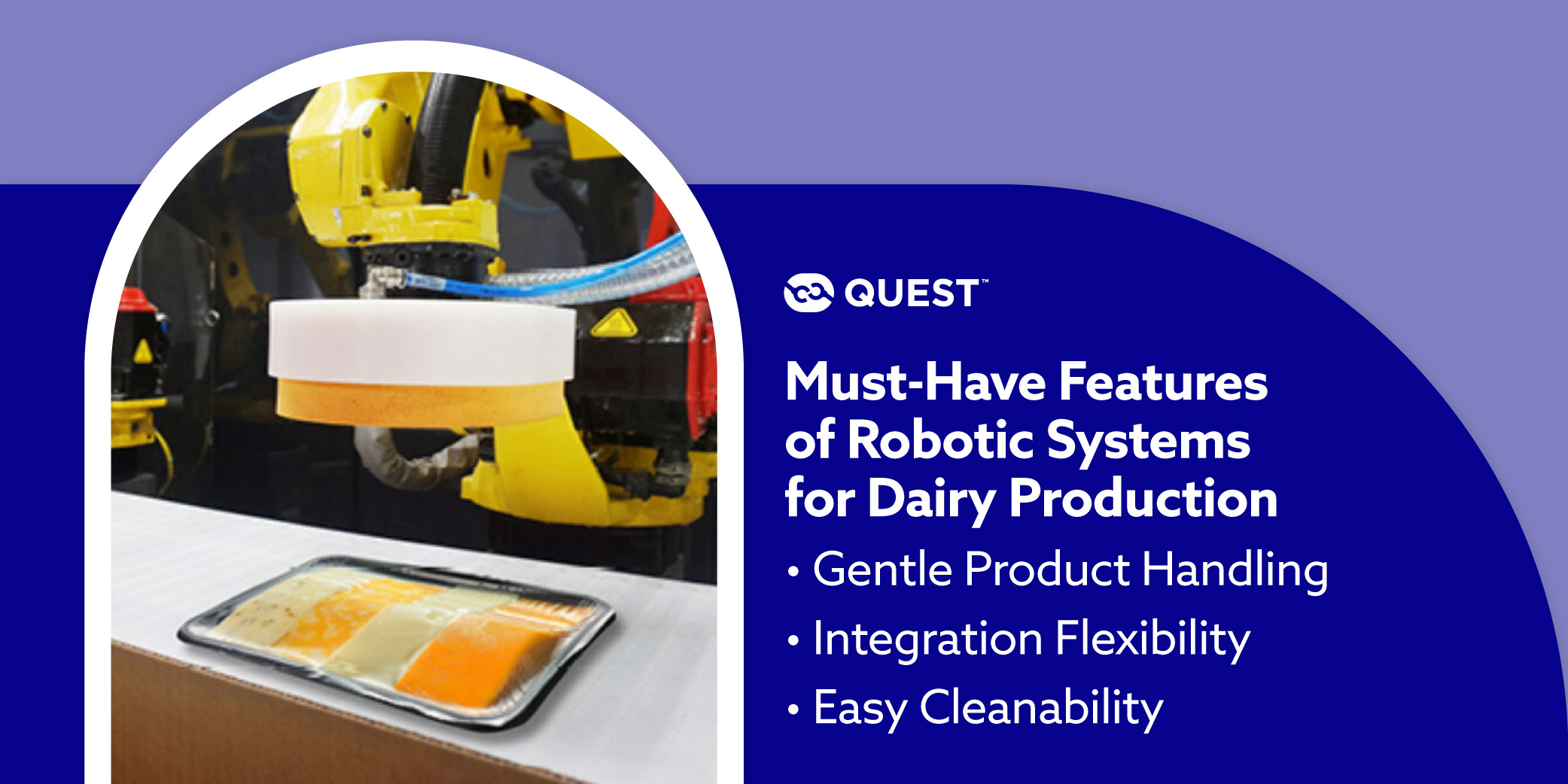
Gentle Product Handling
If you’re packaging goods such as unwrapped cheese or yogurt packs, you may need a primary handling system designed for gentle pickups, packing and movement. This prevents damage from occurring to the packaging without sacrificing speed or productivity overall.
Integration Flexibility
You need a robotics automation that connects with the rest of your equipment, and not necessarily a standalone system. For example, you may wish to investigate a case packing system that accommodates various pack sizes without extensive changeovers or complex workflows.
Easy Cleanability
It should be quick, simple and efficient to thoroughly clean the system to prevent bacteria or contamination from infecting packaged products. An example of this is end-of-line palletizing systems that maintain hygienic standards through the final stage.
This, of course, is not an exhaustive list. It’s imperative to match your sanitary robotics to your unique facility, products and workflow.
Leading the Charge for the Next Era of Dairy Packaging
Automation has become the new “big cheese” for dairy packaging businesses across the country. This brings enhanced sanitation, compliance with food safety regulations and improved operational reliability to companies, regulators and end customers.
Today, countless dairy producers rely on Quest’s robotic solutions to help meet stringent hygiene standards while boosting operational efficiency. It also offers substantial operational improvements, speed throughput and workflow support to businesses struggling to scale while meeting demand.
Dairy, however, is just one piece of the puzzle — there are many other use cases for produce, nuts and seeds, snack foods, and animal protein. Quest is proud to offer a full range of automation products, as well as a long list of industries served, to better serve the needs of primary and secondary packaging markets.
For more information about packaging with robotics, explore our cheese automation solutions.